For Custom Fabric Colors, Go to Sumida-ku
Edo murasaki is a shade of purple with a slight blue tint. Theater aficionados in Japan know it as the color of the cloth wrapped around the head of Sukeroku, the lead character in the popular Kabuki play of the same name. It is one of many hues that can truly be called a traditional Tokyo color.
By Local Creators' Market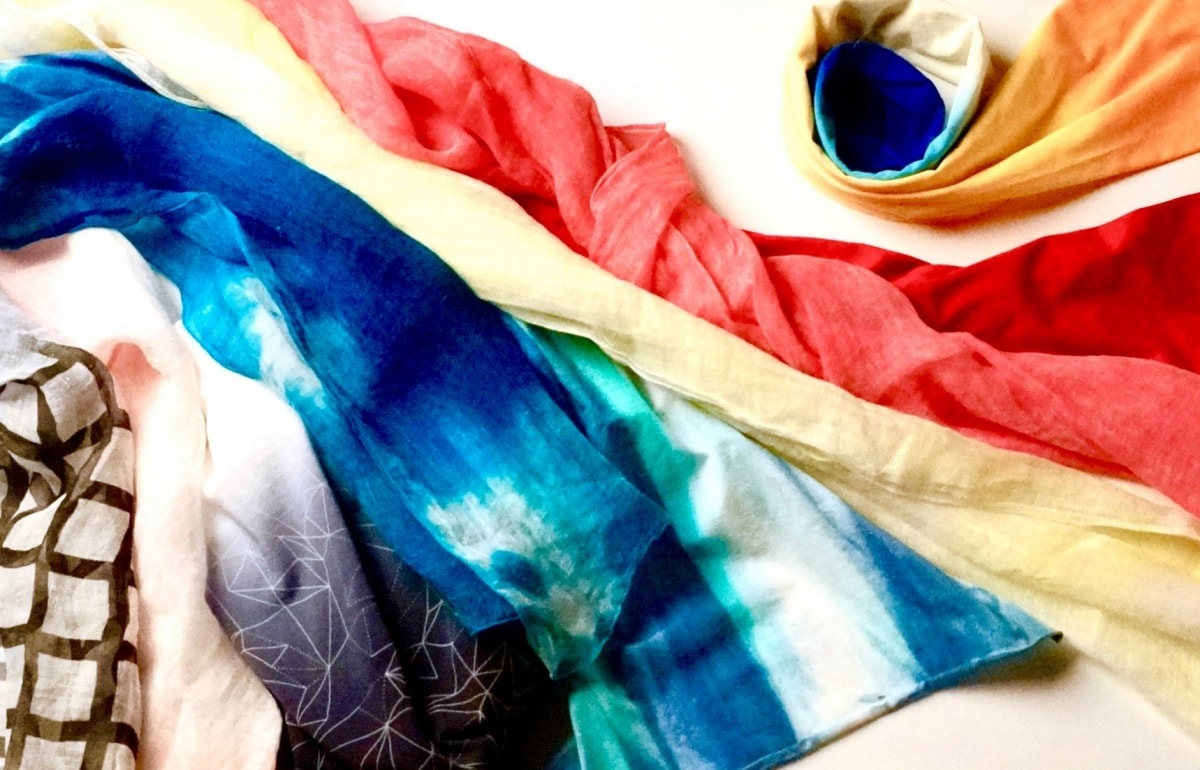
http://local-creators-market.com/tokyo/
But what colors could possibly characterize the Tokyo of today—a teeming metropolis and cosmopolitan mishmash of fashion that glitters with a vast palette of hues and tints? A number of hand-dyeing shops are striving to recreate that full spectrum, producing colors with remarkable accuracy and speed.
Place an order with a swatch or color chip, and the shop will delve into a formidable databank of colors amassed over the history of the craft to instantly dye your fabric to the exact color of the sample. It’s even possible for a client to send undyed fabric and a color sample by courier and receive the dyed cloth on the same day. In Tokyo’s concentrated apparel industry, where exhibitions open and close constantly, this is an invaluable service.
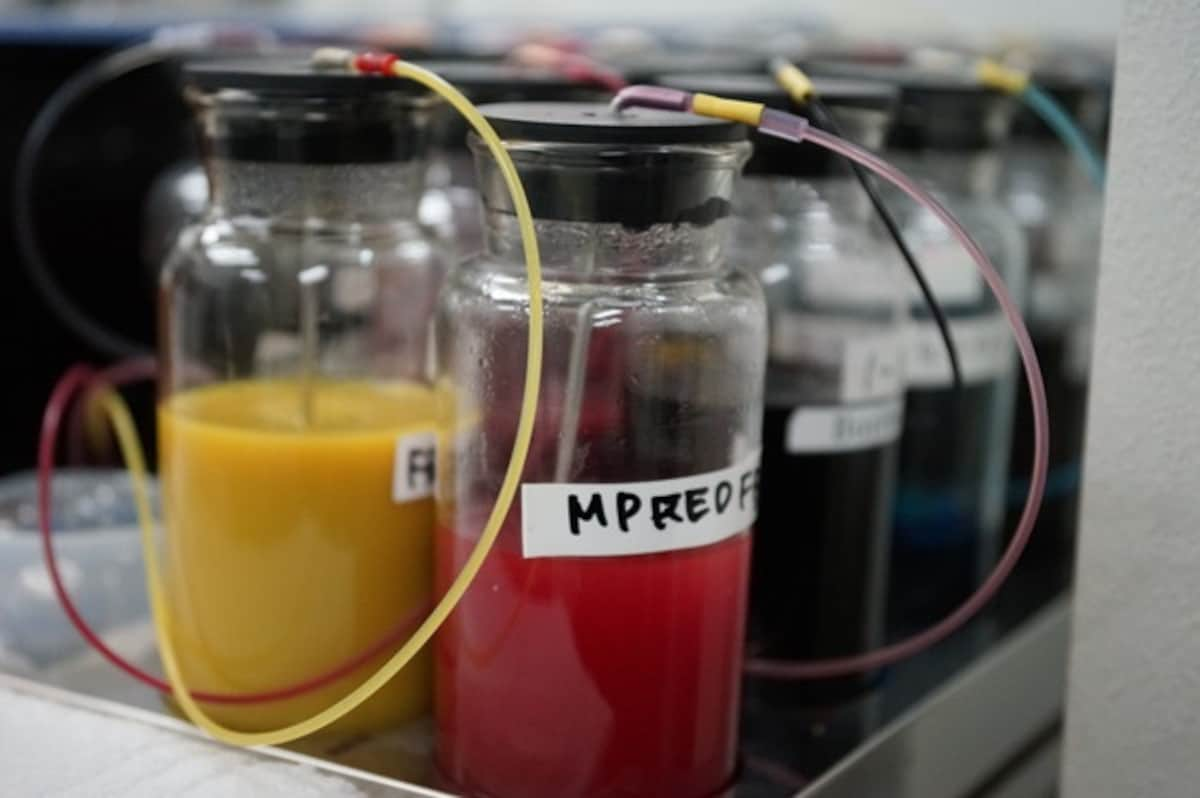
In fabric dyeing the mixing and matching of color draws on the three primary colors red, yellow, and blue—except for special cases like emerald green, for example, which is rendered by blending a vivid blue-tinged yellow with turquoise blue. The complexities multiply exponentially from there. Even the same dye will look different when applied to different kinds of fabrics, and apparel makers today often mix fabrics and textures in the same article of clothing.
Once a fabric is washed after dyeing, the look of its color changes again. These concerns make colorant blending a complex task indeed, as dyers need to account for subtle changes that occur when the fabric is washed to set the dyes. A neutral gray or beige, in which the three primary colors must be evenly balanced, will turn pink if there is too much red, or appear green if there is too much blue.
And so the motherlode of past data, as well as the artisan’s skill in measuring and mixing, is essential to rendering any given color. While some shops, like Uchida Dyeing Works, use computers and spectrophotometers for efficiency measuring and mixing pigments to within 0.0001 percent of a kilogram, in the end the final product depends on the eyes of the people guiding the process. As any dyer will tell you, “We know what to do as soon as we see the color sample.”
Hand dyeing also makes it possible to fill small-lot custom orders for 10 to 20 items, a task the larger factories with batteries of dyeing machines are unable to do. Uchida Dyeing Works employs a dozen or so craftsmen, each responsible for five to six dyeing vats that can rotate between orders twice daily. Though small in size, the studio can dye more than 100 different items in a single day.
Buyers in Japan are unforgiving when colors fade before their time—or worse, bleed—as that is considered low-quality workmanship. With small-batch hand-dyeing of original or one-of-a-kind items, the pressure is especially high to yield exactly the right result. Nevertheless, Sumida’s seasoned craftsmen settle into their task matter-of-factly, turning out an endless spectrum of colors.