Learning to Make Japan's Most Durable Washi Paper
Hand-made washi, once Japan's standard paper material, is still produced in workshops large and small across Japan. An artisanal product especially prized by artists and interior decorators, it comes in a wide variety of colors, sizes and thicknesses and is made from different ingredients, depending on the region where it is produced.
By Vicki L BeyerMaking Nishinouchi Washi Paper
The production method of Nishinouchi Washi of Ibaraki Prefecture has resulted in an especially tough paper that has lent itself to particularly interesting uses.
The Kaminosato Museum in Hitachiomiya has a gallery of products made with Nishinouchi Washi and offers workshops for visitors who want to try their hand at papermaking or learn more.
The key ingredient of Nishinouchi Washi is nasu kozo, a variety of the paper mulberry. Nishinouchi Washi uses the central core of the plant’s branches, processing it by steaming, drying, boiling and beating until what’s left is a mass of soft, silky fibers. These are mixed with water in a large, square tub to form a thick slurry, the basic material of washi production.
But, as one of the craftsmen at Kaminosato Museum explains, paper made from this slurry would be weak and prone to tearing or even dissolving if it were to get wet. So, a “secret” ingredient is added: tororo paste or Neri. Neri is a slimy, starchy paste made from a ground tuber, the Abelmoschus manihot, more commonly known as sunset muskmallow or, in Japan, tororo aoi. The Neri strengthens and stiffens the washi, giving it an unusual durability.
To make paper from the Neri-fortified slurry, a shallow tray with bamboo screen as its bottom, essentially a form for the paper, is quickly dipped into the slurry, drained off while shaking the screen back and forth to distribute the fibers, dipped again and drained/shaken again. The result is a wet, pulpy mat that, when compressed and dried, becomes a single sheet of washi paper.
With prior arrangement, visitors to the Kaminosato Museum can try their hand in this washi-making experience. Or, they can try their hand at producing washi thread to be woven into cloth.
Making Thread (and Cloth) from Paper
In this part of Japan, using paper threads in cloth production was relatively common in the pre-industrial period. Cotton did not grow well and silk was beyond the means of most common folk, so people devised a way to make thread out of the region’s durable washi, which doesn’t break down when it gets wet, and use that thread to weave cloth.
The process begins from a sheet of washi, into which thin strips are cut with a razor, being careful not to cut all the way to the edge, but leaving the sheet intact with the strips cut into the middle.
These strips are then rolled on a board with the flat of the hand, again and again, occasionally shaken out to prevent tangling. Gradually, the rolling produces threads. The rolling is continued until the threads reach the desired thickness. At this stage, the painstaking process of turning the strips into a single length of thread begins by carefully tearing the end of the sheet connecting two “threads” and rolling that thicker bit of paper between the fingers until two threads have become one longer thread. This is repeated at alternating ends of the sheet until the entire sheet has become a single length of thread.
Obviously the threads can’t be rolled into something as fine as silk thread, and the ultimately produced cloth is much heavier and coarser, more appropriate for the work wear of farmers and laborers. Cloth made entirely out of these paper threads was not unusual, but it was perhaps more common to use cotton or hemp threads for the warp on the loom and paper thread for the weft threads passed back and forth using a shuttle.
The cloth is heavier and coarser, traditionally more appropriate for the work wear of farmers and laborers
In the gallery/shop at the Kaminosato Museum, sheets of Nishinouchi Washi and various items made with it are on display or available for purchase. Wallets and handbags, elaborately dressed dolls or papier mache figurines, boxes and other containers, overall an astonishing variety of products.
Learning to Make a Cochin Lantern from Washi Paper
Thanks to its durability and water-resistant properties, another popular use of Nishinouchi Washi was in the production of chochin paper lanterns, the flashlights and porchlights of the pre-electric age. Chochin lanterns are still used for festivals and special events, as well as to announce the presence of bars and restaurants, but modern variations have become popular items of home décor as well.
Suzumo Chochin in Ibaraki’s Mito city is a gallery style shop offering both traditional and modern styles of chochin lantern. It’s also possible to join a workshop to make a traditional lantern, for those who have always wanted to know the secrets of these soft-glowing portable orbs.
The workshop includes all the materials needed to make a chochin lantern.
The workshop begins with participants selecting a message to be written on their chochin. They often carry messages, announcing their purpose, the name of a proprietor, or even a greeting. This message is inscribed in special, indelible ink onto the sheet of Nishinouchi Washi that will form the skin of the chochin.
Next, participants learn how to set up the collapsible form that holds everything in place while the lantern is being assembled.
Once the form is assembled, bamboo “cuffs” are placed at each end. A small hole has been drilled into each and one end of a long cord-like strip of bamboo known as a higo is placed into this hole. The higo is then wrapped around the form, resting in notches on the form all the way to the cuff at the other end, to become the ribs of the lantern.
Once the ribs are in place, paste is brushed onto them and the cuff at each end and the inscribed piece of washi is gently attached. After the paste has dried, the collapsible form is removed and prefabricated black lacquer caps are placed on each end of the lantern to finish it off. The one for the bottom is solid, which the top one is a ring with a handle attached, so that the lantern is open at the top but can be easily carried. While chochin were once lit by candles affixed to the bottom of the lantern, these days, small battery-powered lights are preferred.
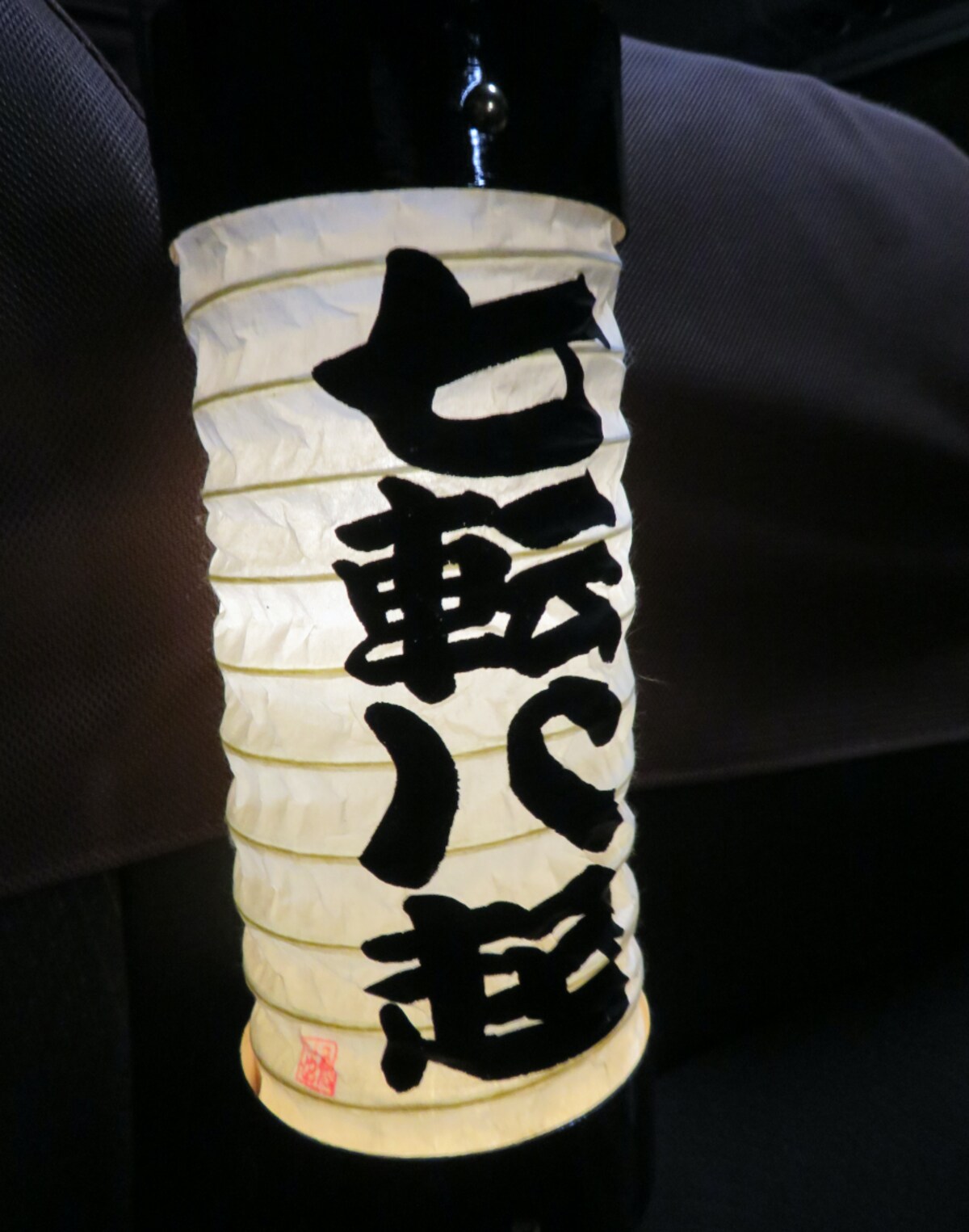
A finished chochin lantern has soft light.
While Nishinouchi Washi is also used to make stationery, window coverings and wallpaper—the more traditional uses—it is fun to discover the wider variety of uses for this very sturdy hand-crafted paper of Ibaraki.
Kaminosato Museum is open daily, except Wednesdays, 9:00-17:30 (also closed across New Year’s). To arrange a paper or paper thread experience, email
kaminosato@spice.ocn.ne.jp
Website:
http://www.kaminosato.com
Suzumo Chochin is open daily, 9:00-18:00 (closed Wednesdays 6/15-7/31). To arrange a chochin experience, email
webmaster@suzumo.com
Website:
https://www.suzumo.com/en/