A One-of-a-Kind Pottery Adventure in Miyagi
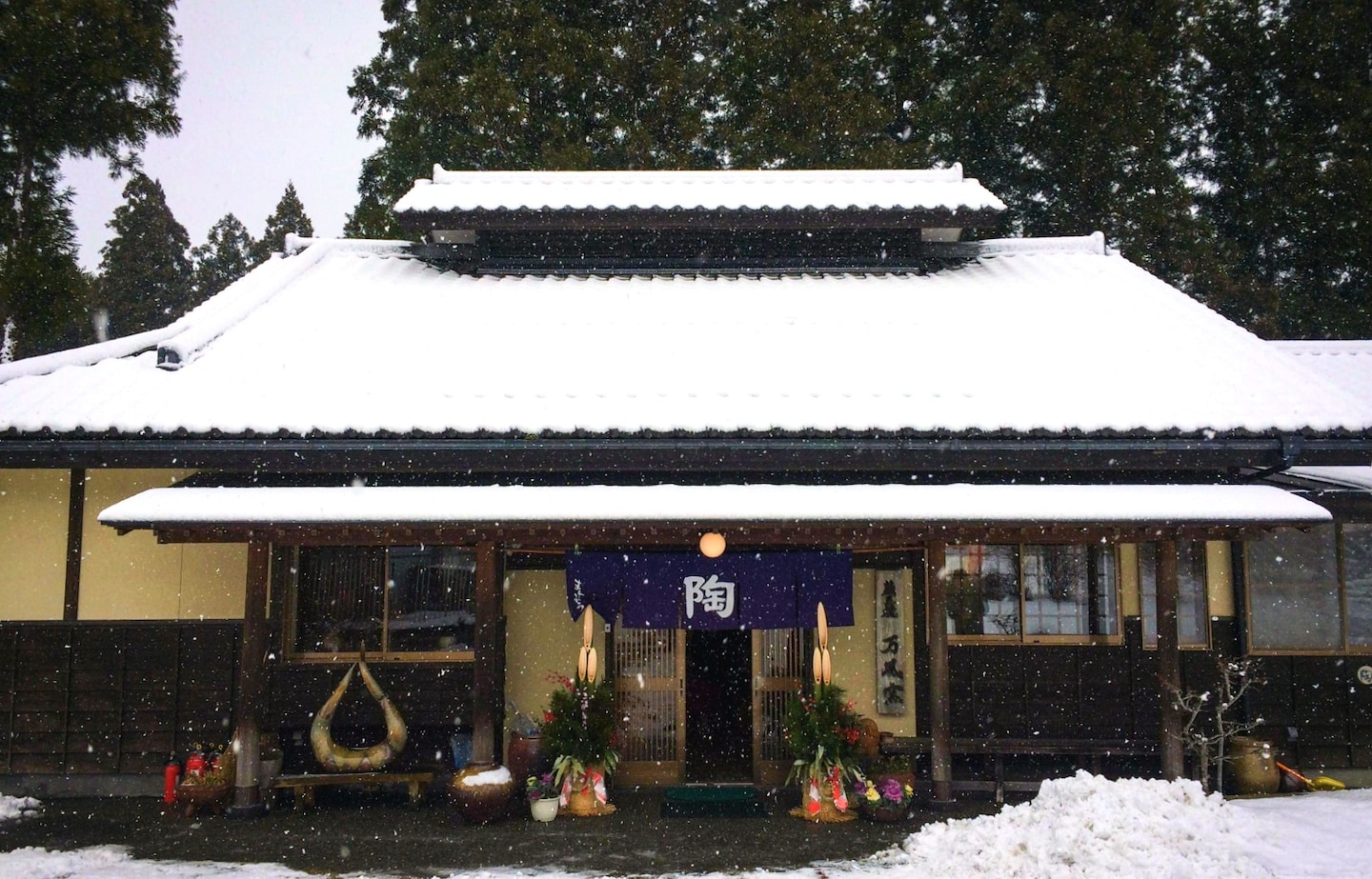
After a final soak in the outdoor natural hot spring at Yunushi Ichijo and stuffing our faces with a healthy and delicious course breakfast, we packed up our things and jumped into the rental car for our next adventure. Day two in Miyagi included something a little different. We were actually going to make our own Zao-yaki pottery.
By Marky Star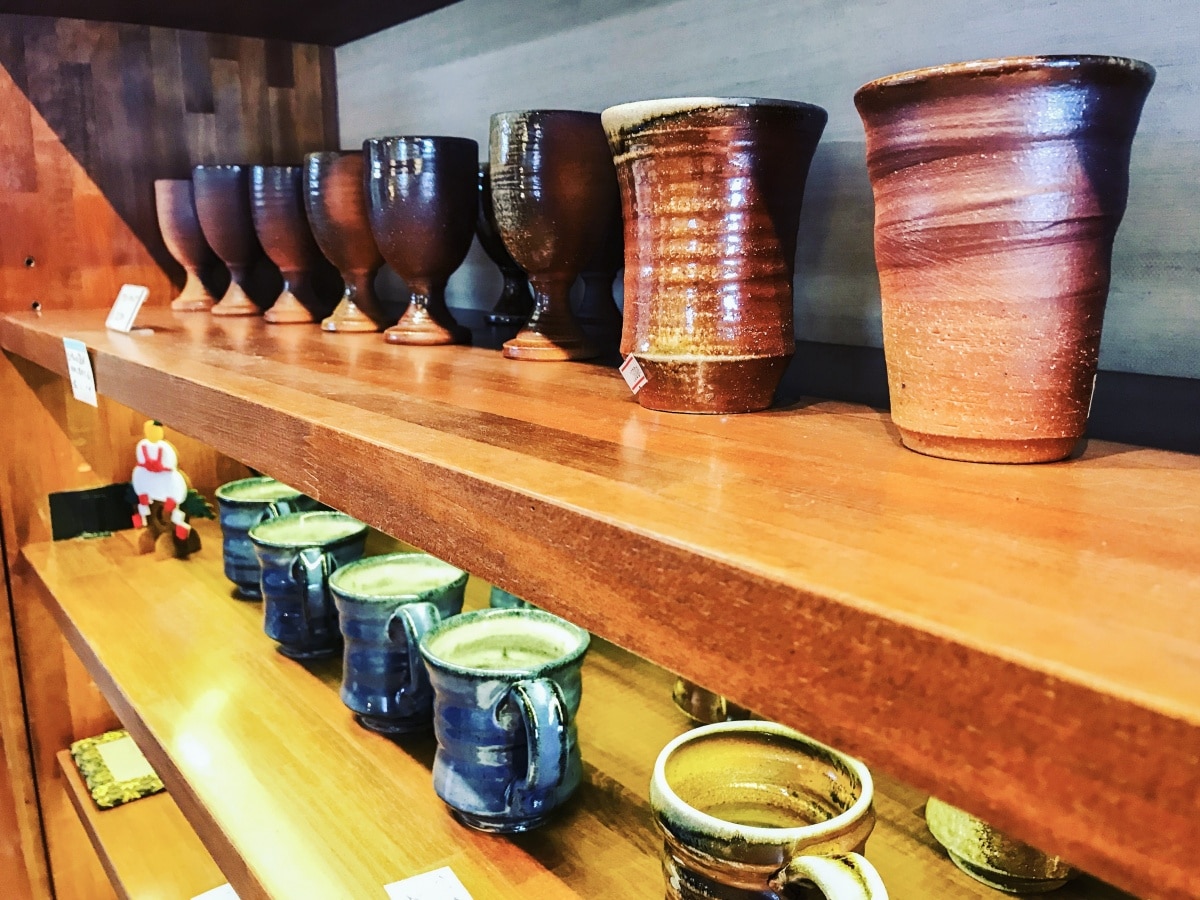
I took a ceramics class once in university and believe me when I say, I was terrible at it. I couldn’t use the potter's wheel for the life of me, so at the end of the semester, all I had to show for it was a collection of hand molded ashtrays that looked like a chain-smoking first grader had made them. Not only were my designs ugly and impractical, I couldn’t even get the glazes to turn out right. All the colors were just hideous. Because of this, I was pretty nervous about trying my hand at pottery again, especially in front of other people.
Manpu Pottery
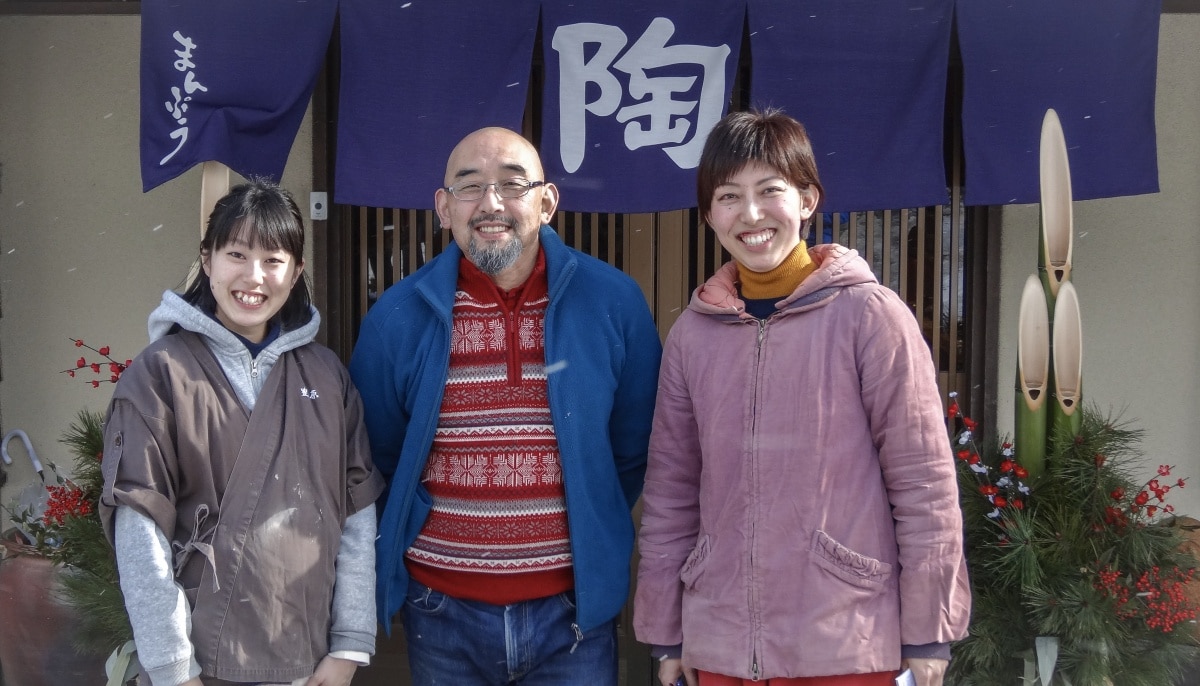
When we arrived at Manpugama (literally, Manpu Pottery), we were greeted in Japanese by the owner and head potter, Toyohara Manpu, and his third daughter, Mamiko. We later learned his eldest daughter, Emiko—who speaks English—was teaching a group of school children in the studio at that time.
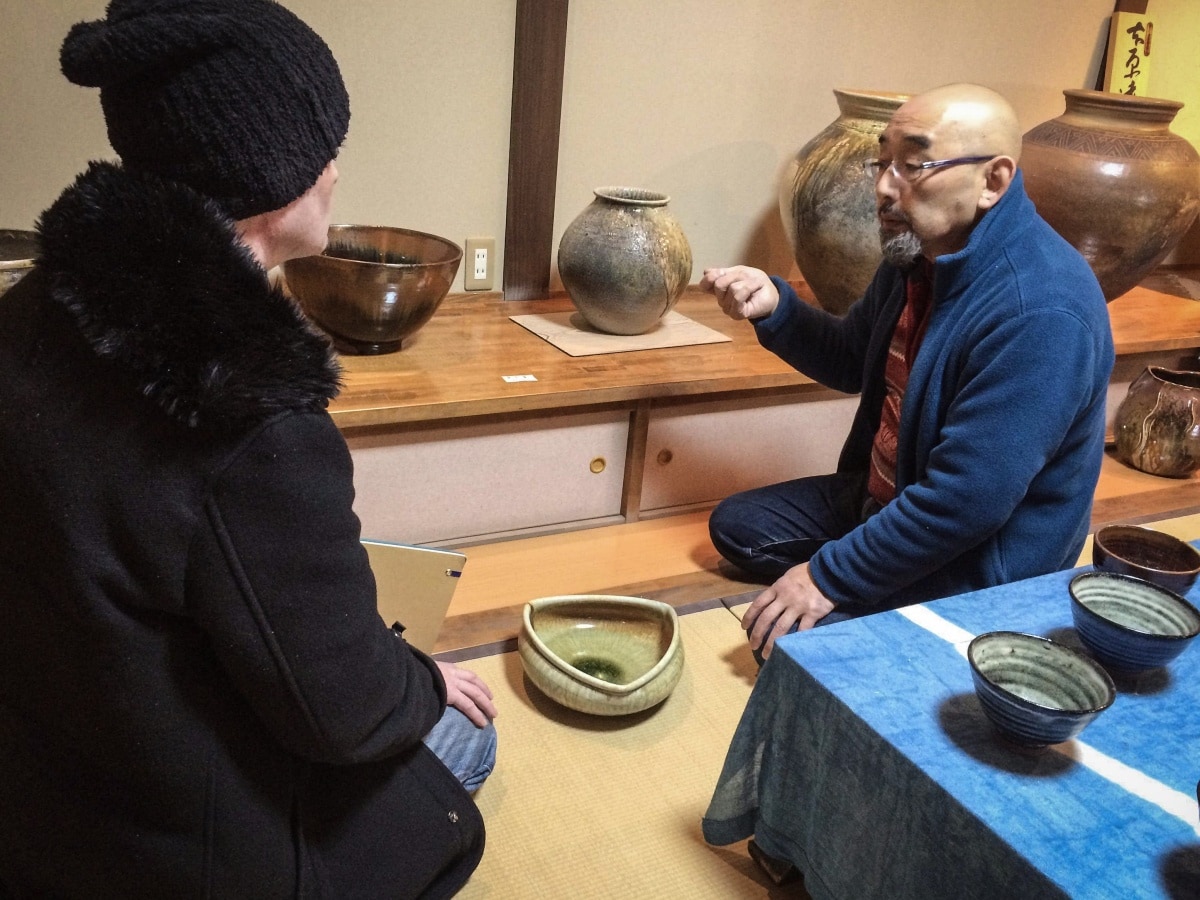
Manpu has operated this studio and gallery here in Miyagi Zao for 30 years. He took us around the gallery and explained the techniques he used. When volcanic ash mixes with wet earth, it produces a red colored clay, this is the type of clay that is found locally and that he and his daughters use for their beautiful works on display. The gallery was filled with everything from teacups to sake decanters and huge vases. Occasionally, he would focus on a few pieces to explain his glazing techniques that reflect the Japanese fondness for unpredictable patterns in traditional ceramics.
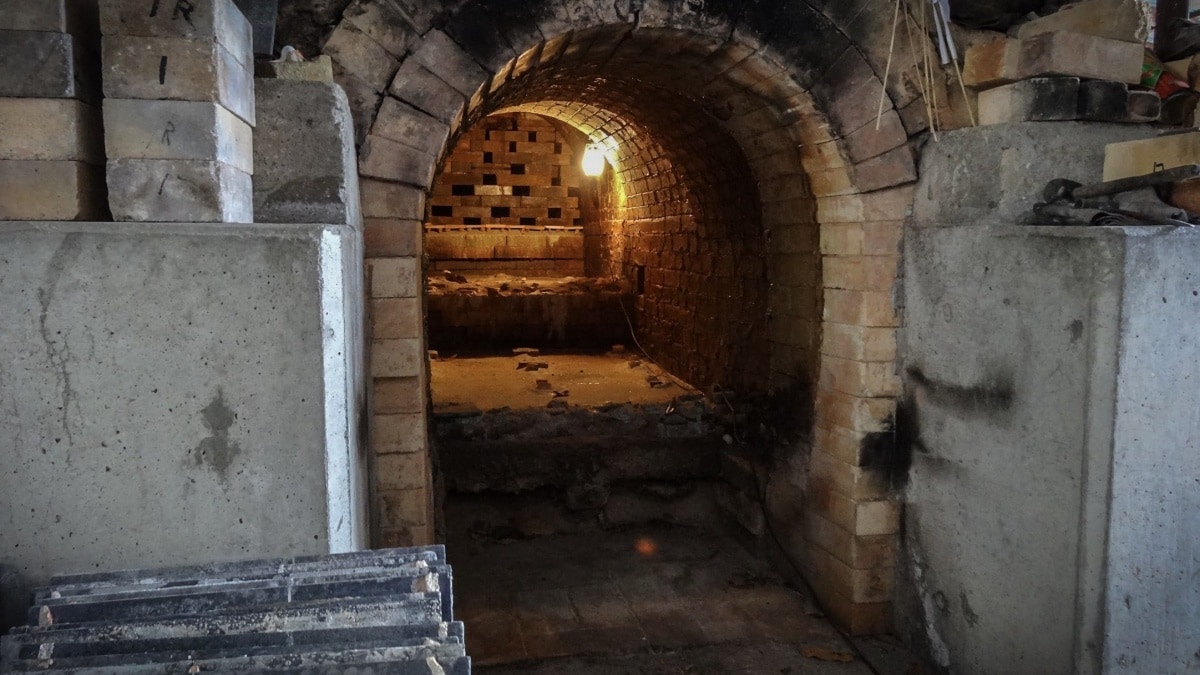
Next Mr. Manpu took us out of the studio to show off his kiln, which is roughly the size of a small one-story house and fires at 1281°C (2337.8°F). Where he places unglazed pieces depends on the colors and types of effects he has planned for each one. He also points out stacks of wood inside the shack protecting the kiln. These are red pines which create a beautiful glass coating that makes the pottery glisten under the light.
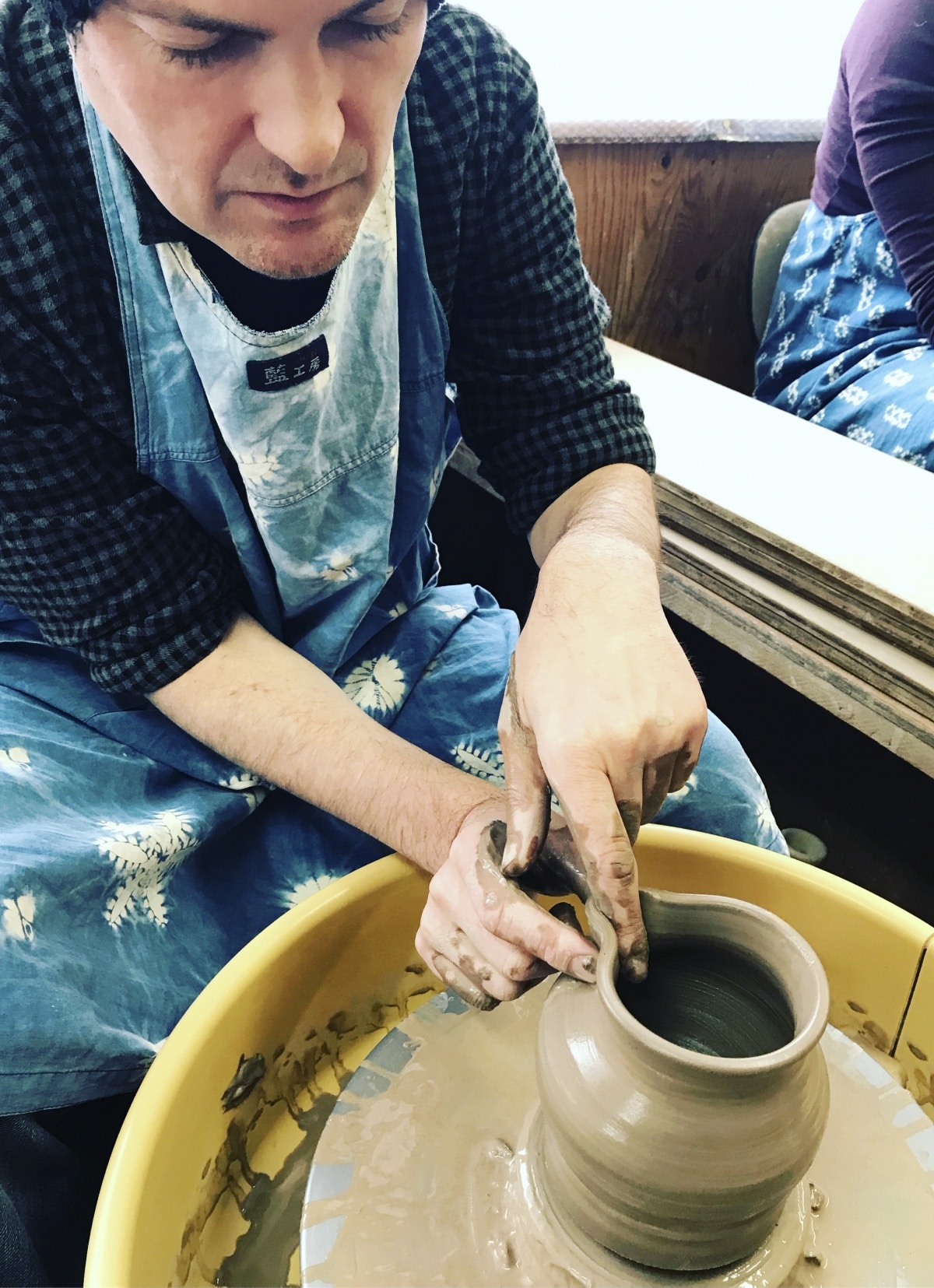
Now it was time to get down to business. He handed us over to his daughter Mamiko who taught us some of the basics of using a pottery wheel. Put your hands together in this shape to elongate things. Use this shape to flatten and round out the clay. Push down like this to open up deep cavities for cups and so on. She got us familiar with the machine and how to control the speed, as well as when to slow down and when to stop completely. Then she assured us that she would be with us for every step of the way, giving tips and tricks, as well as some much-needed encouragement. I said I wanted to make a sake decanter, a sake cup and small serving dish for appetizers.

What started out as nervous fear, soon became a genuine feeling of enjoyment. Granted Mamiko helped me out a lot, but I soon realized that I wasn’t going to make a crappy ashtray that would just get tossed out in the trash (I don’t even smoke, after all). Thanks to her advice and occasional guiding hand, we had five pieces that were good to go.
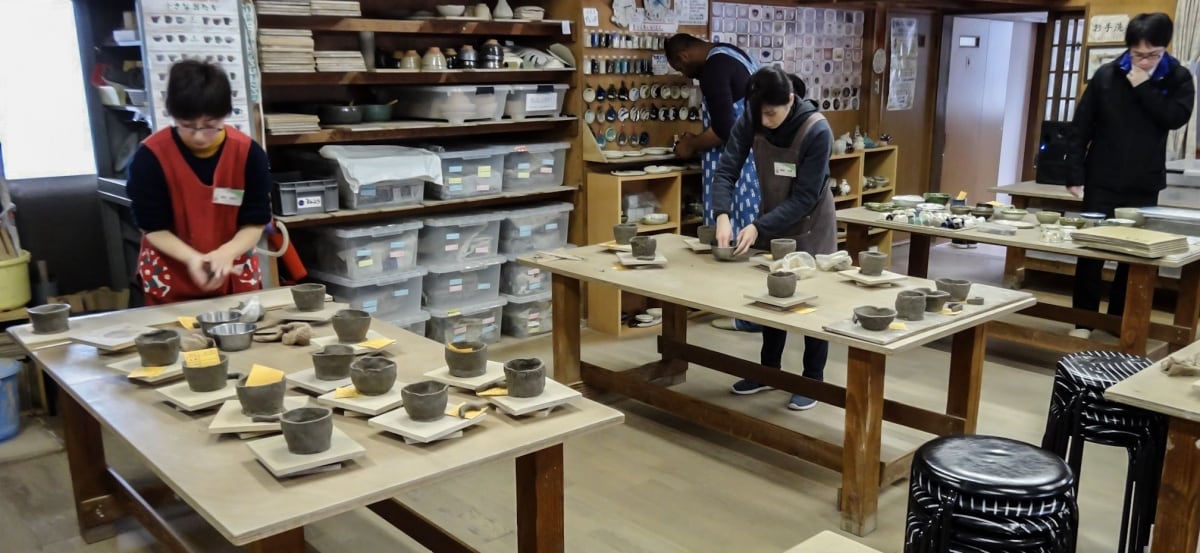
The next stage was picking out glazes. Each piece was allowed a maximum of two colors. We could also choose some simple patterns, such as cherry blossoms, cranes, rabbits and other traditional Japanese imagery to decorate our pottery. They said it would take about two weeks for our pieces to dry completely, then they would be placed into the kiln and the glazes expertly applied. The entire process takes about two months, but once it’s completely finished, Manpugama will box it up securely and ship it to your home.
We took our time leaving, being sure to thank the Toyohara family for all their help and for answering all of the questions about Zao-yaki. We also took a few pictures in front of their studio gallery and then said our goodbyes. We’ll have to update this article when we get the finished goods!